Danish researchers have developed a wide variety of products and technologies aimed at assisting that country’s farmers, and by extension, those across the globe, to lower their carbon footprints and employ more environmentally friendly production practices.
Measuring feed and milk output
A large percentage of any dairy farmer’s variable costs are feed-related, and in Denmark the portion is as high as 88%. Any saving in feed or improvement in feed efficiency therefore goes a long way towards increasing profits.
Genetics play a major role in feed conversion. Selecting the best-performing animals, however, is easier said than done. VikingGenetics, a co-operative owned by 20 000 dairy and beef farmers in Denmark, Sweden and Finland, has therefore developed technology to make the process of selection simpler and more accurate.
The co-op’s cattle feed intake (CFIT) system uses 3D cameras and artificial intelligence to monitor the feed intake of each cow during lactation. A camera, placed above the feeding table, identifies a cow through her unique colour pattern and shape, estimates her weight, and quantifies how much she eats.
The cameras then take photographs of the feed surface area to analyse consumption throughout the day. One image is taken before the cow gets to the feeding table, and another after she has left it; the system then compares the two images to calculate how much a specific cow has eaten. The process is repeated daily for all cows in the herd.
Since each cow’s milk output is also measured, an accurate figure can be provided to reflect production. Over time, the data can be used to select the cows that have the best feed conversion ratios. Also available is a body condition scoring system, which notifies the farmer if the animal deviates from her ideal body condition at any stage of lactation.
Jakob Voergaard, senior breeding product manager at VikingGenetics, adds that besides being an effective data collection tool for improved feed efficiency via breeding, CFIT can be utilised to manage cow behaviour, feeding and health.
Green fertiliser
The drive to lower the carbon footprint of food production has forced players across the value chain to seek areas where reductions are possible. Since nitrogen fertiliser makes up a major part of a farmer’s carbon footprint, research into reducing the impact of this aspect is receiving considerable attention.
Danish fertiliser company Yara has introduced a fertiliser that replaces ammonia manufactured from fossil fuels with ammonia made with renewable electricity. This green fertiliser is a nitrate-based mineral substance with a chemical composition identical to that of fertilisers produced from fossil fuels (natural gas, coal and oil). To produce it, Yara uses electrolysis to extract the hydrogen needed to make the ammonia from water.
The product is currently available in Norway, the Netherlands and Australia, and there are plans for further global expansion in 2023.
The technology has enabled Yara to reduce fertiliser production emissions from nitrous oxide (N2O), a potent greenhouse gas (GHG), by more than 90%. Wheat production’s carbon footprint can be cut by 20%, resulting in a 12% lower carbon footprint per loaf of bread.
Birgitte Holter, vice-president for green and low-carbon fertiliser solutions at Yara, notes that green fertiliser is a fossil-free and effortless way to decarbonise food production.
“Hundreds of food companies have pledged ambitious targets to reduce their carbon footprints, and they need to be aided by everyone in the value chain, including farmers,” she says.
Holter adds that while Yara’s green fertiliser comes at a higher price, rising conventional fertiliser prices, looming carbon taxes, and consumer focus on carbon footprints will make it increasingly attractive.
“If the cost of the green fertiliser had to be passed on to the consumer, we’d be looking at €0,50 [about R8,50] extra for a loaf of bread, which isn’t much.”
Farmers using manure as fertiliser can also look forward to a lowered carbon footprint and better yields, thanks to technology from German multinational chemical manufacturer BASF. The company has developed an additive, Vizura, which, when combined with manure slurry, slows the conversion of ammonia into nitrate. This reduces nitrogen losses from nitrate leaching and can reduce N2O emissions by 50%, according to the company.
Karel van de Velde, senior sustainability manager at BASF, explains that nitrogen is converted to nitrate in the soil, with the rate of this process depending on temperature, soil moisture level and soil condition.
“Adding Vizura significantly delays this conversion, meaning that ammonia is available to the plants for longer, resulting in a yield increase of up to 7% in maize and 5% in wheat.”
The better absorption rate of the nitrogen in the slurry also means that less slurry is needed. Trials showed that slurry applications could be reduced from 58t/ha to 39t/ha. The technology therefore not only reduces emissions, but cuts fertiliser costs, too.
Ploughing robots
While labour on farms is more readily available in South Africa, the need for greater efficiency in low-skilled, repetitive tasks matches that of Europe. Developers of agri-robots have therefore focused on tasks such as ploughing, weeding, seeding and spraying.
AgroIntelli, a leading Danish agricultural robotics company, has launched an autonomous robotic system called Robotti that can take care of all these tasks, freeing up labour to focus on higher-skilled jobs.
Robotti can be used on a range of crops, including onions, salad plants, leeks, potatoes, carrots, parsnips, strawberries and pumpkins. Any farming implement up to 3m wide can be attached to Robotti, so ploughing, mowing, seeding, spraying, weeding or ridging can all be carried out autonomously.
The machine can be monitored remotely from a smartphone, and notifies the farmer if it stops unexpectedly. When creating a field plan, the software registers notes all known obstructions such as fences, power poles and bushes, and the machine stops immediately should it encounter an unexpected obstacle.
Jakob Bebe, AgroIntelli’s chief commercial officer, explains that Robotti can cover about 1ha/hour, depending on the task, and can run 24 hours/day, as it is equipped with lights for night driving.
“Robotti runs on biofuel, so the carbon footprint is reduced. And at 3 000kg, it weighs less than a tractor, which means less soil compaction,” he adds.
Robotti is priced at around €180 000 (R3 million), and Bebe says that a farmer can expect a return on investment in less than two years.
Biochar captures carbon
Biochar is known to improve soil, reduce nitrogen leaching and increase production. Now a company in Denmark is producing biochar from livestock manure, which not only captures carbon, but produces biofuel as well.
SkyClean uses a process called pyrolysis, where manure (or any plant residue) is heated to about 600°C without oxygen. It then emits gas and is charred. In the pyrolysis process, half of the carbon in the waste is converted to biochar, while the other half becomes oil and gas. The gas can be used as biofuel and the oil can be refined into fuel for the transport sector. The pyrolysis also eliminates methane from the feedstock.
When slurry or manure is applied to lands, the remains of antibiotics, pesticides, hormone-like substances and microplastics that occur in it tend to become concentrated in the soil. Pyrolysis breaks down these residues to harmless molecules, so that when the biochar is spread, no harmful substances are added to the soil.
Henrik Stiesdal, founder of SkyClean, says that among carbon-negative technologies, atmospheric clean-up through biochar sequestration stands out as a safe, cost-effective, and technologically feasible solution.
“The production of biochar in this manner solves three major climate change challenges: the need for significantly reduced GHG emissions from agriculture, the need for the capture and sequestration of atmospheric carbon, and the need for carbon-neutral fuels for transportation.”
While SkyClean currently operates a single biochar plant in Denmark, Stiesdal says the technology can be deployed at any location where organic feedstock is readily available.
Seaweed for feed
Antioxidants and tannins in seaweed have been found to impede the development of methane, which, as noted, is a notorious GHG. Danish researchers are therefore involved in a project called Climate Feed, which is seeking to develop a feed supplement that contains seaweed, and thereby reduce cows’ methane emissions by up to 30%.
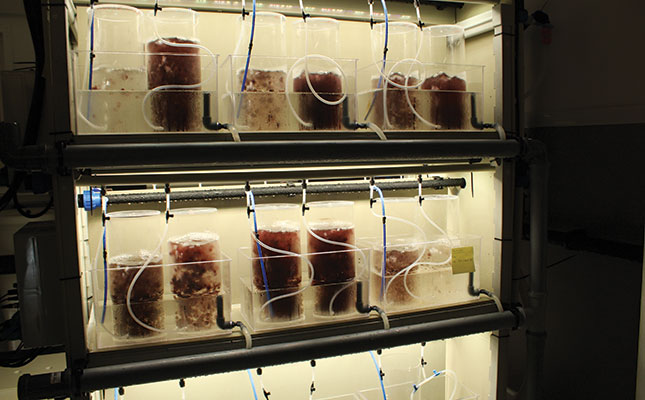
This reduction will do much to help the Danish Agriculture & Food Council’s vision to make food production climate-neutral by 2050.
The project aims to develop methods for cultivating, harvesting and processing seaweed into a finished product, such as powder or pellets, for farmers to add to feed.
While Denmark has an extensive coastline, seaweed is not abundant, and the National Institute of Aquatic Resources (DTU Aqua) is currently in the process of researching best practices to reseed fjords with sugar kelp and dulse seaweed. The former is a good feed source for pigs, while dulse, dubbed the ‘bacon of the sea’, is sought after by vegan chefs.
Mette Nielsen, a researcher at DTU Aqua, explains that nets seeded with spores of seaweed are placed in tanks for six to eight weeks. By then, the seaweed will have grown sufficiently to be placed in the fjords, and here it is allowed to grow out over eight months, after which it is harvested.
Once DTU Aqua’s codes of best practice have been finalised, commercial seaweed farms will be established to scale up production. The waters of the fjords are nutrient-rich, partly due to extensive nitrogen run-off from farms, so the seaweed requires little to flourish, feeding off water nutrients and sunlight. It therefore presents an ideal food for both animals and humans.
Food of the future
While meat is still very much on the menu in Africa, there is a strong move towards veganism in Europe, and the increase in demand for vegan food products has created opportunities for farming alternative crops.
Soya bean has long dominated plant-based protein products, but food manufacturers are increasingly looking towards yellow peas and fava beans as a tastier alternative. Since European consumers are wary of soya bean products, labelling them as the cause of large-scale deforestation, especially in the Amazon, peas and beans pose an attractive alternative.
Ulrich Kern-Hansen, founder of Danish company Organic Plant Protein, which manufactures meat-equivalent products, says these products require a protein concentrate of at least 55%.
“Yellow peas and fava beans fit the bill, and through a process in which a high-temperature extruder is used to shape the final product, the proteins are textured and the digestibility
of the proteins from the peas and the beans is improved.”
Kern-Hansen notes that hybrid products, where at least some of the meat is replaced by textured plant proteins, have huge potential.
“The climatic impact of these products is reduced by up to 50%, they’re cheaper than meat products, and they hold the same protein content,” he says.
The products, sold under the Plant Mate brand, are made without using water, chemicals or protein isolate. The last of these is seen as having a high carbon footprint, so for climate-conscious consumers, it is undesirable.
In addition, many plant-based proteins include not only isolate, but also a lengthy list of ingredients, most of which mean little to consumers. The notorious ‘E’ numbers, which refer to a host of often artificial and undesired ingredients in food, also feature regularly.
New technology, such as that used by Organic Plant Protein, enables protein nuggets to be produced with only two ingredients, making these meat alternatives more appealing to consumers.
Email Jakob Voergaard at javoe@vikinggenetics.com, Karel van de Velde at karel.vandevelde@basf.com, Jakob Bebe at jmb@agrointelli.com, Henrik Stiesdal at info@stiesdal.com, Birgitte Holter at vibeke.laroi@yara.com, Mette Nielsen at menie@aqua.dtu.dk, or Ulrich Kern-Hansen at ukh@OrganicPlantProtein.dk.